Jul 2022
Are you maximising or just manufacturing your data?
Manufacturing has remained consistent since the days of Henry Ford’s production line. That is, until the digital revolution.
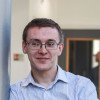
Lead Solutions Architect: Unified Comms
Now, the industry can harness technology to not only facilitate cost and production efficiencies, but to access, analyse and act upon data like never before, enabling firms to plan and implement business growth.
What would I use?
If you’re in manufacturing, you’re likely aware of – if not using – a SCADA (Supervisory control and data acquisition) or DCS (Distributed Control System) system.
They both allow you to shift from manual to digital production methods, improving efficiency through automation; a prime example being all machine data available on one screen, rather than someone walking round a plant each hour to check manually.
While both systems control plant operations and the devices within them, DCS systems are focused on process control, but don’t tend to reach beyond that.
SCADA systems on the other hand not only assist with the day-to-day production in a facility, but also prioritise the collection and understanding of data at the same time.
Data in manufacturing
Albert Einstein said: “Any fool can know, the point is to understand”. And this is true within any business, across any industry; having the data is one thing, understanding it another, and acting upon it something else entirely.
Within manufacturing, the data you can gather can be used in a variety of ways.
It can help you to understand when and why there are period of down time, where issues or errors are occurring, or simply to look at the entire chain of events across a process to individually assess each function and element.
For example, a steel beam manufacturer discovered that every day, some of the beams were coming off the line slightly twisted. There could be many explanations for this; changes in shift patterns, temperature changes heading into day or night, even perhaps when more of the team took smoke or lunch breaks.
Without a system to gather and analyse the data, it was simply conjecture that could lead to months – even years – of trial and error to find out the reasoning and implement change, all while valuable product is being wasted.
The reason was something no one considered: the tide. The production facility was based next to the North Sea coast and as the tide rose and fell, it made very slight changes to the land on which the factory was sat.
This still took a number of months and lots of head scratching to unearth, but the use of a SCADA system meant that accessing the historical data was immediate.
Of course, this is an extreme example but it demonstrates a point – that you don’t know until you look.
Ultimately, using the data isn’t about being reactive to solve a problem that arises, but to give you the ability to experiment. Can changing the temperature of one element by 2 degrees save costs without affecting production times or quality? What about speeding up the conveyors by 0.002mph?
Use it to make the most of your product, team and time.
Are there any risks?
Risk comes hand in hand with innovation, and digital elements add even more to that.
If SCADA and DCS systems are online it means they, like anything from a website to personal emails, are at risk of a cyberattack.
As your manufacturing and production facility systems are not a standalone element of your business, but connect with other elements and departments, it’s key for these to be linked for wider operational efficiency. But by joining these company-wide dots, you need to consider greater security.
Linking your SCADA system to your wider IT infrastructure is an obvious thing to do to make sure anyone who needs it can access the data collected, or systems in play. But it is vital to ensure these are monitored by an expert to ensure that they can be easily unlinked in the event of an attack.
How you use your SCADA system can alter the extent to which an attack impacts your business. For example, in March 2021 threat actors targeted a water facility in Nevada. While hackers were able to use malware to affect the SCADA and backup systems, as these were used only for data monitoring and visibility, the full industrial control system was not affected and continued to operate as normal. On the other hand, an attack in Maine resulted in a water treatment system being operated manually for an extended period until the SCADA computer was restored.
Ultimately, your manufacturing site is where your profit lies and without it operating at full capacity, your business is at risk, whether that’s from understaffing, lack of raw materials or a result of a cyberattack.
If you have processes in place to counter any eventuality, your business will survive. If you use the data at hand to improve, drive efficiency and develop, it will thrive.
For more information on how you can maximise the data you are creating, speak to our team today by emailing info@waterstons.com, or find out more about our services here. Here are our technology consulting services.